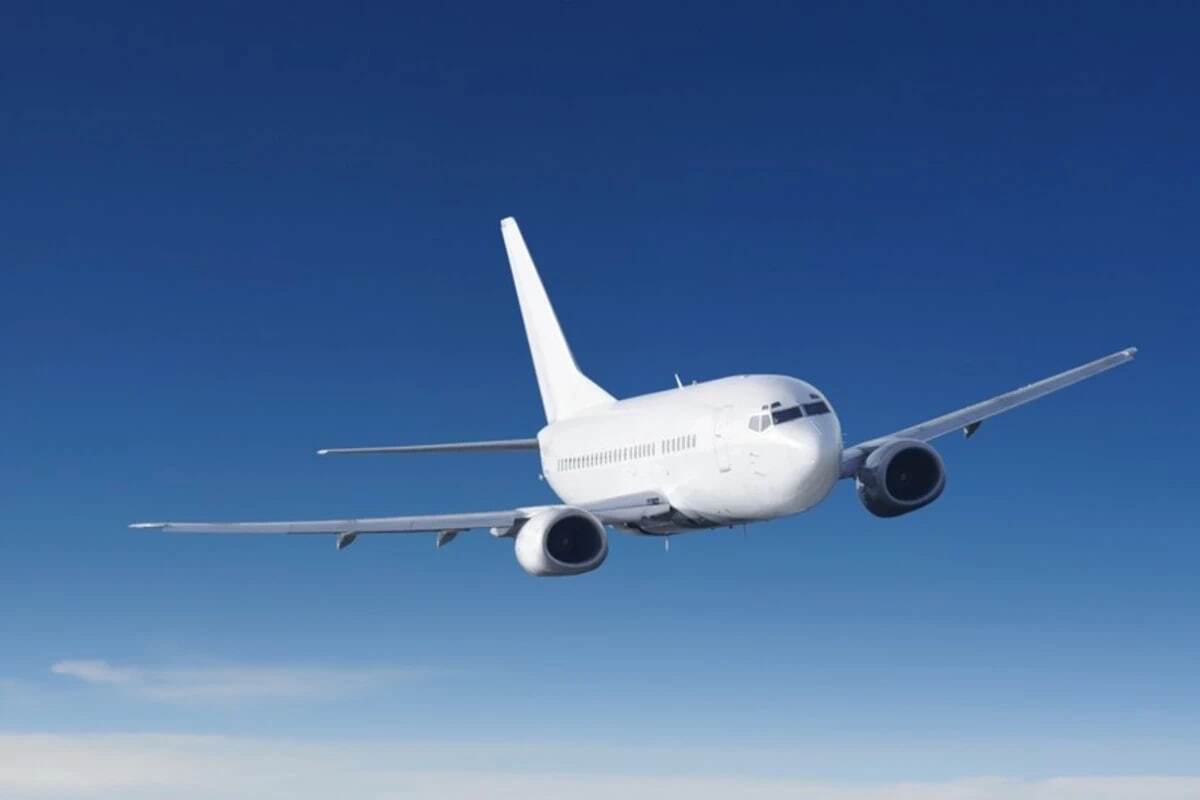
Tabriz Refinery Taking Measures to Compete With International Rivals
EghtesadOnline: Tabriz Oil Refinery in East Azarbaijan Province has invested $500 million in development projects over the last 10 years to be able to compete with rivals in international markets, managing director of the company said.
“Development plans carried out during the period include boosting crude processing capacity, building diesel refinery units, producing a wide range of lubricants, installing hydrogen pressure swing adsorption systems and constructing sulfur recovery units,” Gholamreza Baqeri was also quoted as saying by IRNA.
In addition to refining oil, the company produces at least 40 types of products ranging from gasoline compliant with Euro-5 and Euro-4 standards, diesel, jet fuel, naphtha, butane, hexane, kerosene, vacuum bottom, benzene, tar and antifreeze to various kinds of petrochemical catalysts.
“The initiatives are in line with objectives to become Asia’s largest oil refinery and have a say in global markets,” he added.
Located in southwest Tabriz over 150 hectares, Tabriz Oil Refinery was established in 1978. It has a refining capacity of over 110,000 barrels of crude per day that accounts for 7% of Iran’s total oil processing capacity.
Asmari oilfields in the southwestern Khuzestan Province supply crude oil to the refinery.
The refinery is currently the most important supplier of feedstock to Tabriz Petrochemical Company.
Baqeri said Tabriz Oil Refinery has signed a contract worth $20 million with Ghadir Energy and Power Investment Company, based on which the latter is obliged to provide the former with electricity infrastructure so that the refining complex can generate its own power.
Another development project at the refinery is to reduce its mazut production. The refinery currently produces 1.4 million tons per year of mazut, which is primarily used as feedstock for tar.
The refinery is expected to reduce mazut production from around 25% of its output to below 5% by 2022.
“A new cooling tower at the refinery has been completed after three years,” he said.
“The cooling unit, slated to use foreign parts and equipment worth $7 million, was constructed with domestic equipment and cost $5 million.”
Baqeri noted that since the refinery had increased oil treatment units, it also needed a new cooling tower to supply water.
In oil and gas refineries, industrial equipment is often jacketed or sleeved with flowing water to cool fluids and absorb process heat. This equipment generates a large heat load that can disrupt operations if not properly handled. Cooling towers are used to cool this process water for reuse.
CO2, SO2 Emissions
In related news, IRNA quoted Hamed Armanfar, the head of Tehran Oil Refinery, as saying that his company reduced its CO2 and SO2 emissions by 50,000 tons and 2,500 tons respectively in 2020.
“Energy consumption in the refinery declined by 1.1% last year, helping the firm save $40 million in annual spending,” he added.
Tehran Oil Refining Company has been introduced by the National Iranian Oil Refining and Distribution Company as the top refiner in terms of measures taken to help preserve the environment.
The ranking came after surveys by NIORDC based on various criteria, including green space, wastewater, air pollutants and energy management.
According to environmental laws, industries and production units should allocate 10% of their total area to green space. In addition to complying with regulations, Tehran Oil Refinery has 293 hectares of green space.
Regarding sewage treatment, the refinery increased the capacity of its wastewater treatment unit to 11,000 cubic meters per day and plans to use treated wastewater instead of the local water supply.
The plan to transfer sewage from South Tehran Wastewater Treatment Complex to Tehran Oil Refining Company is underway and when completed, 19 million cubic meters of sewage a year will be diverted to the refinery’s wastewater unit. Treated wastewater will be used for cooling towers and in the refinery’s fire department.
To reduce air pollutants, the huge refinery south of Tehran uses natural gas as feedstock in furnaces and boilers. In the past, it used liquid fuels like mazut that are a major source of pollution. It also has installed oxygen analyzers on furnaces and boilers to control the combustion process and reduce gas consumption.
The refinery has launched a nitrogen production unit to improve health and environmental standards.
With the capacity to produce 1,200 cubic meters of nitrogen per hour, the unit will help replace natural gas with nitrogen in storage tanks to prevent possible hazards from flammable liquids.